Getting the Right Image
New X-ray Instrument Keeps Up the Global-leading High-resolution 3D Imaging Research in Metallurgical Engineering at the University of Utah
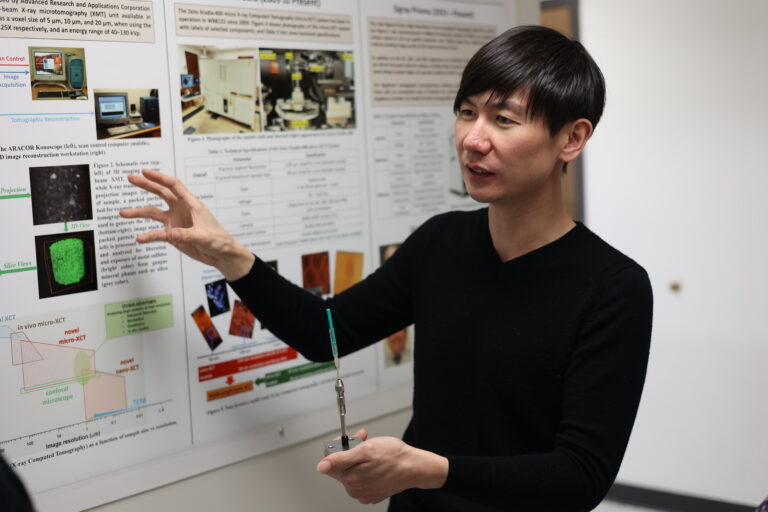
Jin in front of the XRM-900 in the William Browning building.
Credits: Todd Anderson
Assistant Professor of Metallurgical Engineering in the U's Department of Materials Science and Engineering Jiaqi Jin recently took delivery of a new X-ray instrument, the first of its kind.
The acquisition arrived just in time, underscoring Jin's 2023 Freeport-McMoRan, Inc. Career Development Grant from the Society for Mining, Metallurgy & Exploration (SME). The recognitions was for his research expertise, teaching contribution, and service in the mining community. Using X-ray Computed Tomography (CT) in 3D characterization of particulate systems is an important aspect of Jin’s research work. And this newly arrived X-ray instrument will significantly strengthen his capability in mineral processing studies, which also maintains the U's metallurgical engineering program as arguably the best in the country.
In a recent tour of the equipment deployed in December in the Browning Building at the U, Jin explained the history of 3D imaging in the field of mineral processing from its early stages at the flagship university. “In the very beginning, our research group collaborated with the Ford Motor Company,” said Jin. “Some automobile parts were produced by casting, and Ford used micro X-ray CT to image defects (gas holes) inside the parts. We sent our mineral samples to Ford. They [would] scan it, send the image back, then we processed and analyzed them for our mineralogy study.”
In 1996, NSF funding was secured by the department’s Miller group to buy the U’s first instrument of micro X-ray CT. This ARACOR Konoscope had a resolution of the art voxel (pixel in 3D) size imaging 20, 10, and 5 μm. Later, an Xradia-400 micro X-ray CT system was installed by the same group in 2009. (Miller retired in 2023 after 55 years of service at the U.) The micro X-ray CT instrument was also called “X-ray microscopes” (XRM). Inside a big lead box, the source, sample, X-ray optics, and camera are aligned on rails for different magnifications of high-resolution 3D imaging. This Xradia-400 XRM, which will continue to be used for the time being at the Jin lab,has been used to scan samples at the smallest voxel size of 1.8 μm in practice. The Xradia series uses a “two-stage magnification” approach (sealed X-ray tube and an objective magnification detector) to generate a small effective detector pixel but is limited some by low detector efficiency and costly source replacement.
Patent-pending Architecture
Now, the new X-ray CT instrument, called the EclipseXRM-900TM, introduces a patent-pending architecture to achieve its breakthrough resolution capabilities, offering both 0.3 μm (300 nm) resolution and the highest resolution for large working distances (large samples). This achievement is enabled by both the minimized source spot size (novel open X-ray tube with state-of-the-art electron optics) and the minimized effective detector pixel size (large pixel count flat panel detector).
Jin has been using X-ray CT to characterize the multiphase particles, which provides important 3D information on mineral liberation, exposure, particle damage, and pore network analysis of packed particle beds such as those encountered in heap leaching or dewatering. This new technology will enable his group to study finer features of minerals and, ultimately, will be more economical in the case of mining for metal extraction with better energy efficiency.
The manufacturer of the equipment, Sigray, Inc., deploys powerful, synchrotron-grade research capabilities to bring to market laboratory X-ray systems. Their products include X-ray absorption spectroscopy, high-resolution X-ray fluorescence 2D elemental imaging and high-resolution X-ray CT for 3D imaging. These research facilities, as with the U’s, are often tasked with 2D or 3D imaging the samples at the best quality and at the fastest acquisition times.
Quantitative Information from 3D Images
In the discipline of metallurgical engineering, which recently moved to the College of Science, it’s all about getting the right image. And for Jin’s team, that includes scanning a variety of different samples, such as the porous structures architected by material chemists. These structures are then reconstructed and transformed into 3D digital images to show remarkable contrast and details of the nanopores.
“The important part [of our work] is about image processing and analysis,” said Jin. “Besides the fancy-looking 3D pictures, what quantitative information can you extract out of the scans?” That's what the past 30 years have been about for the metallurgical engineering team at the U: to develop the expertise and algorithm to run the analysis, “so that they [scans] actually provide value.” The new EclipseXRM-900TM will make that happen more efficiently and more broadly.
by David Pace