Metallurgical Engineering Professors Sign a $10M/10-year Research Agreement
Updates:
(January 3, 2024): Metallurgical Engineering Professors in the Department of Materials
Science and Engineering at the University of Utah recently signed a research agreement
with IperionX (IPX) for $10MM over ten years, effective January 1, 2024. The project
is led by Z. Zak Fang (PI) and Pei Sun (Co-PI). The Charlotte, NC-based IPX aims to
become a leading American titanium (Ti) and critical materials company – using patented
metals technologies to produce high-performance Ti metal from Ti minerals or scrap
Ti at lower energy, cost, and carbon emissions than conventional technologies. Fang
and his research team will provide IPX with research and development services related
to metallurgical technologies to produce primary metals, advanced manufacturing technologies,
including additive manufacturing (i.e., 3D printing) of titanium alloys, and recycling
of rare earth metals from magnets used in wind turbines and electric vehicles. “This
academic-industry partnership of the Fang Lab and IperionX exemplifies the College
of Science’s innovative bench-to-application research to meet the needs of our energy
future,” said Dean Peter Trapa.
(November 17, 2023): Zhigang Zak Fang’s research is one of R&D 100 Winners announced
by R&D World magazine. This renowned worldwide science and innovation competition,
celebrating its 61st year, received entries from 15 different countries and regions.
This year’s esteemed judging panel included 45 well-respected industry professionals
from across the world. Fang’s research was cited in the Process/Prototyping category.
Original post (September 2023):
Zhigang Zak Fang: Humboldt Award
Titanium (Ti) metal, prized for its high strength-to-weight ratio, corrosion resistance and biocompatibility is a critical material in aerospace, defense, and medical applications, but its wider use is obstructed by excessively high costs.
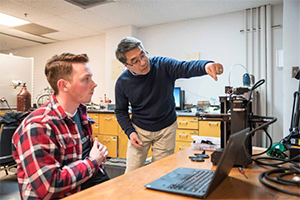
Fang discussing with a former student Jarom Chamberlain, Ph.D., about 3D printing.
That’s where Materials Sciences and Metallurgical Engineering Professor Zhigang Zak Fang comes into play. A recent recipient of the prestigious Humboldt Research Award, Fang has developed a breakthrough technology that can produce high-quality, low-carbon emitting titanium powder at a significantly reduced cost. Known as the Hydrogen Assisted Metallothermic Reduction (HAMR) process, the technology developed by Fang is based on the discovery of new science about the effects of hydrogen on the stability of Ti solid solutions with high oxygen content (up to 14wt%.)
“Titanium metal is difficult to produce because of its strong affinity to oxygen,” says Fang, who was notified earlier this month about the Humboldt, which promotes scientific cooperation between research institutions in the U.S. and Germany. He discovered that the bond between titanium and oxygen can be destabilized by inserting hydrogen atoms into the Titanium(II) oxide (Ti-O) solid solution lattices, leading to the completely new approach for sustainably producing low oxygen titanium with minimum energy and cost.
“By dramatically reducing the cost and carbon dioxide emissions of producing titanium powder, the HAMR process has the potential to fundamentally disrupt and transform the global titanium metal industry,” continues Fang.
Today, the U.S. must import almost 100% of the “titanium sponge” it consumes each year, made by this older process that is inefficient, expensive, and energy intensive. China and Russia control ~70% of the global market for titanium sponge, creating a significant supply chain vulnerability for a metal critical to America’s national defense. The current market-standard process for creating titanium metal heats titanium ore to 1,800 degrees Fahrenheit and reacts with chlorine gas and petroleum coke to produce titanium tetrachloride. That chemical compound is purified, reduced by molten magnesium in an argon atmosphere for up to four days, and then vacuum-distilled into the porous, brittle form of titanium known as “sponge. It is then crushed and melted to make ingots and other titanium mill deliverables that are sent to the manufacturers of titanium products.
Fang’s research which led to the HAMR technology, promises to improve energy efficiency drastically. The HAMR process can produce primary titanium metal from either minerals or from titanium scrap. Recycling titanium scrap is the focus of the initial commercialization by IperionX, a commercial entity engaged in mining, production, and reshoring of Ti manufacturing in the US. Producing low-oxygen spherical titanium powder from scrap is accomplished by utilizing HAMR in combination with a patented Granulation, Sintering, and Deoxygenation (GSD) process. The result is that high-oxygen titanium scrap is transformed into low-oxygen titanium powders that meet or exceed stringent aerospace and biomedical industry standards.
Titanium powder can be used for additive manufacturing or utilized by powder metallurgy to manufacture products in a broad range of demanding applications, including aerospace, defense, biomedical, and other civilian applications, with dramatically increased sustainability.
An internationally renowned scientist
Every year, the Alexander von Humboldt Foundation grants up to 100 Humboldt Research Awards to internationally leading researchers of all disciplines from abroad in recognition of their academic record to date. The Humboldt Prize, also known as the Humboldt Research Award with a cash prize of EURO 60,000, is given annually to internationally renowned scientists and scholars and is named after the late Prussian naturalist and explorer Alexander von Humboldt.
Inventor of a series of process technologies, Fang is a globally recognized innovator in the areas of cemented tungsten carbide, refractory metals, titanium, powder metallurgy, and metal hydride for hydrogen and thermal energy storage. Prior to joining the U, Fang had a successful industrial R&D career for over a decade. He has authored or co-authored over 180 peer reviewed publications. He is the named sole or co-inventor in over 60 issued U.S. patents. He founded/co-founded two start-up companies and successfully commercialized several tungsten carbide and titanium technologies.
The Humboldt is far from Zak Fang’s first acknowledgment for his work. He is a Fellow of the National Academy of Inventors, ASM, and APMI, respectively. In 2009 he was the winner of an R&D100 Award. He is also the Editor-in-Chief for the International Journal of Refractory Metals & Hard Metals, the flagship scientific journal for refractory metals.
by David Pace | article originally featured on science.utah.edu